Production of Pharmaceutical Creams and Ointments
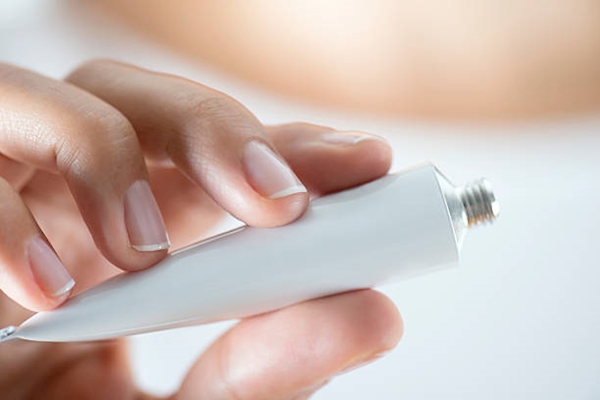
Production of Pharmaceutical Creams and Ointments
Pharmaceutical preparations for treatment of conditions such as rashes, skin irritation, stings, fungal infections, etc. are normally supplied in the form of a cream or ointment as this provides an effective means of delivering the active ingredient directly to the required area. Products can be either a water in oil (w/o) or oil in water (o/w) emulsion, consisting of waxes, emollients and lubricants dispersed in an oil phase, and a water phase containing emulsifying, stabilizing and thickening agents, preservatives and in some cases, colorant. Active ingredients are dispersed in either phase or added when the emulsion has been formed and allowed to cool.
The Process
Ingredients, formulation and product viscosity differ widely, however, a typical manufacturing process breaks down into four individual operations:
• Preparation of the oil phase. Flake/powder ingredients, sometimes dry blended in advance, are dispersed into mineral oil or silicone oil. Heating may be required to melt some ingredients.
• Hydration of aqueous phase ingredients. Emulsifiers, thickeners and stabilizers are dispersed into water in a separate vessel. Heating may be required to accelerate hydration.
• Forming the Emulsion. The two phases are blended under vigorous agitation to form the emulsion.
• Dispersion of the Active Ingredient. The active ingredient often makes up only a small proportion of the formulation; this must be efficiently dispersed to maximize yield and product effectiveness.
The Problem
Using conventional agitators a number of problems can be encountered:
• When added to water, thickening, stabilizing and emulsifying ingredients can form agglomerates which agitators cannot break down.
• Similarly oil phase ingredients can form lumps which require shear to disperse.
• Ingredients must be fully hydrated to obtain the required viscosity and develop yield.
• Partially hydrated materials can build up on the vessel wall, in-tank baffles and parts of the agitator.
• Agitators cannot sufficiently reduce droplet size to form a stable emulsion.
• Active ingredients can be temperature sensitive. Cooling of the product before adding the active ingredient further increases processing time.
• Poor dispersion of the active ingredient impairs product effectiveness.
• Long mixing times and additional equipment may be required to obtain a homogeneous and stable finished product.
The Solution
Arkan Felez mixer can rapidly disperse solids into liquids, hydrate thickening and stabilizing agents, break down agglomerates, and finely reduce particle and globule size to form stable emulsions and suspensions. Mixing times are dramatically reduced, while product uniformity and consistency are greatly improved.
The Advantages
• Stable emulsion.
• Agglomerate-free mix.
• Dramatically reduced mixing time.
• Maximized yield of raw materials as thickening agents are fully hydrated and other ingredients fully dispersed.
• In-tank baffles are not required, improving vessel hygiene.
• Pre-mixing of powdered ingredients can be eliminated.
• The aqueous phase can be produced at ambient temperatures, reducing heating costs. This also accelerates cooling of the mixture, further reducing process
time and costs.
• Consistent product quality and repeatability.
Vacumm Mixer Homognizers of Arkan Felez Company