Production of Cosmetic Creams and Lotions
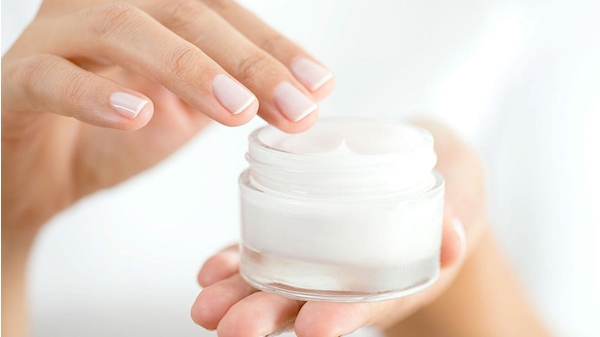
Production of Cosmetic Creams and Lotions
Cosmetic creams and lotions are used for a variety of purposes such as cleansing and moisturizing. The ingredients of these will be different according to the desired use, however to some extent the basic manufacturing process is the same.
The Process
Products can be either an oil-in-water or water-in-oil emulsion, consisting of emollients and lubricants dispersed in an oil phase, and a water phase containing emulsifying and thickening agents, perfume, color and preservatives. Active ingredients are dispersed in either phase depending on the raw materials and the desired properties of the end product. A typical manufacturing process would be as follows:
• Flake/powder ingredients, such as cetyl alcohol and stearic acid, sometimes dry blended in advance, are dispersed into the oil phase. Heating may be required to melt some of the ingredients.
• Active ingredients are dispersed in the appropriate phase.
• The water phase, containing emulsifiers and stabilizers such as Veegum® or Carbopol®, is prepared separately.
• The two phases are then mixed to form an emulsion. This is aided by heating to between 110-185˚F (45-85˚C) depending on the formulation and viscosity.
• Mixing is continued until the end product is homogeneous.
The Problem
Using conventional agitators a number of problems can be encountered:
• Some ingredients can form agglomerates which conventional agitators cannot break down.
• Hydration of thickening and suspending agents is one of the most difficult of all mixing operations. Agglomerates can easily form and some ingredients require shear in order to develop their desired properties.
• When adding powdered ingredients to the vessel, partially hydrated materials can build up on the vessel wall and parts of the agitator.
• Agitators cannot easily form stable emulsions even when the oil and water phases have been heated.
• Long process times and additional equipment are often required to achieve a homogeneous product.
The Solution
Intermediate stages of production can be eliminated, product quality improved and processing times dramatically reduced by using a Arkan Felez High Shear mixer.
The Advantages
. Consistent product quality and repeatability.
• Agglomerate-free mix.
• Stable emulsion.
• Rapid mixing time.
• Maximized yield of raw materials as thickening agents are fully hydrated and other ingredients fully dispersed.
Vacumm Mixer Homognizers of Arkan Felez Company