Pump
Multi-stage homogenizer
Suitable substitute for colloidal mill and piston homogenizers
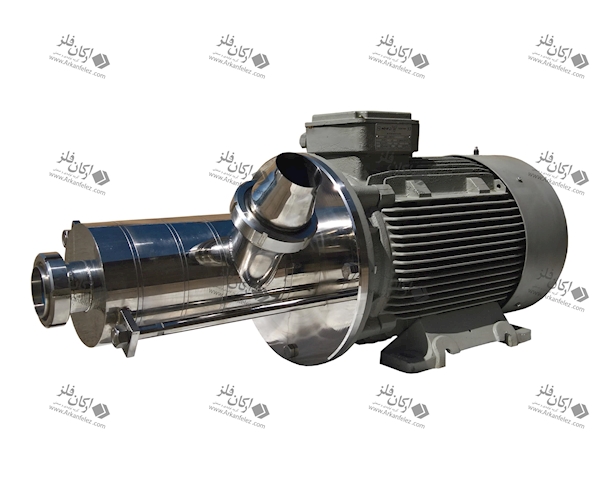
Multi-stage homogenizer model MSH-40
Copied from the product of the German company YTRON
Applications
Food industry: tomato paste line equipment, ketchup sauce, mayonnaise and mustard sauce, juice and concentrate, flavoring emulsions
Cosmetics industry: cosmetic creams, hair dye
Pharmaceutical industry: Pharmaceutical ointments
Chemical industry: polymers, diluting SLES
In conventional methods, fruit juice concentrate is prepared by piston homogenizers at a pressure of about 100 atmospheres. The high cost of purchasing a piston homogenizer, the very high energy consumption, as well as the ancillary costs of consumable parts and expensive maintenance repairs are all problematic points of using piston homogenizers. In addition, the possibility that the taste of the juice will metallize due to the very high pressure is not far from the mind.
The structure of the multi-stage homogenizer is such that the juice is subjected to shear stress 11 times by passing it through the rotor-stator only once to ensure the achievement of the appropriate texture and particle size.
The use of a multi-stage homogenizer for all types of fruit juice ensures equal or better results than the above-mentioned conventional method.
In the RS series homogenizer pump, part of the engine power is spent on circulating products. However, in these homogenizers, all the power of the motor is used to apply very high shear stress to the product and the task of circulating the material is assigned to the feed pump.
By passing the product through this homogenizer only once, it is subjected to shear stress 11 times and the maximum reduction of particle dimensions is achieved. Therefore, unlike the RS series homogenizer pump, which works in batch, it has the ability to work continuously.
Options
- Suitable substitute for colloidal mill and piston homogenizers
- Ability to work 24 hours a day, 7 days a week
- Design in accordance with GMP principles and CIP and SIP capabilities
- All parts in contact with the material are made of 316L steel
- Capacity of about 5000 to 20,000 liters per hour depending on the viscosity of the material as well as the volumetric flow of the feed pump
- Use of a powerful 30 kW electric motor (40 hp) - 3000 rpm
- Has 3 sets of rotors - stators with nested compartments (Multi Chamber)
- Minimum slack between all rotor-stator shear surfaces
- Ability to operate under vacuum or under pressure
Download Catalog
Keywords
Related News
Sending Comments
Most Visited